Throughout the design phase, the provided simulation services allow an optimization of engine concepts in terms of efficiency and power output, as well as a deeper understanding of the thermodynamic processes within the engine. Ideally, these simulations should be performed prior to time- and cost-intensive hardware tests. In addition to the development of new engine concepts, we also offer analyses of existing aggregates, which do not comply with modified objectives regarding emissions, consumption and power output in order to determine necessary measures to achieve performance levels in accordance with the newly-defined priorities
- all combustion engines and their application ranges
- generators, automotive, marine, racing, etc.
1D-engine cycle simulation
The 1D-engine cycle simulation is useful for the analyses of relatively simple technical processes and basic examination of engine concepts in particular. In addition to the examination of stationary engine operation conditions, it is also possible to simulate the dynamic behavior regarding torque and exhaust aftertreatment.
Typical scope of work:
Analysis of engine concepts
- Performance
- Fuel Economy
- Knock control
- one or multi-stage turbocharger
- Dual Fuel
- EGR Strategy
- CAT/DPF/SCR
Optimization of intake and exhaust systems
- Valve timing
- Lengths and diameters of the piping
Turbocharger matching
- Efficiency analysis
- Selecting the suitable turbocharger configuration
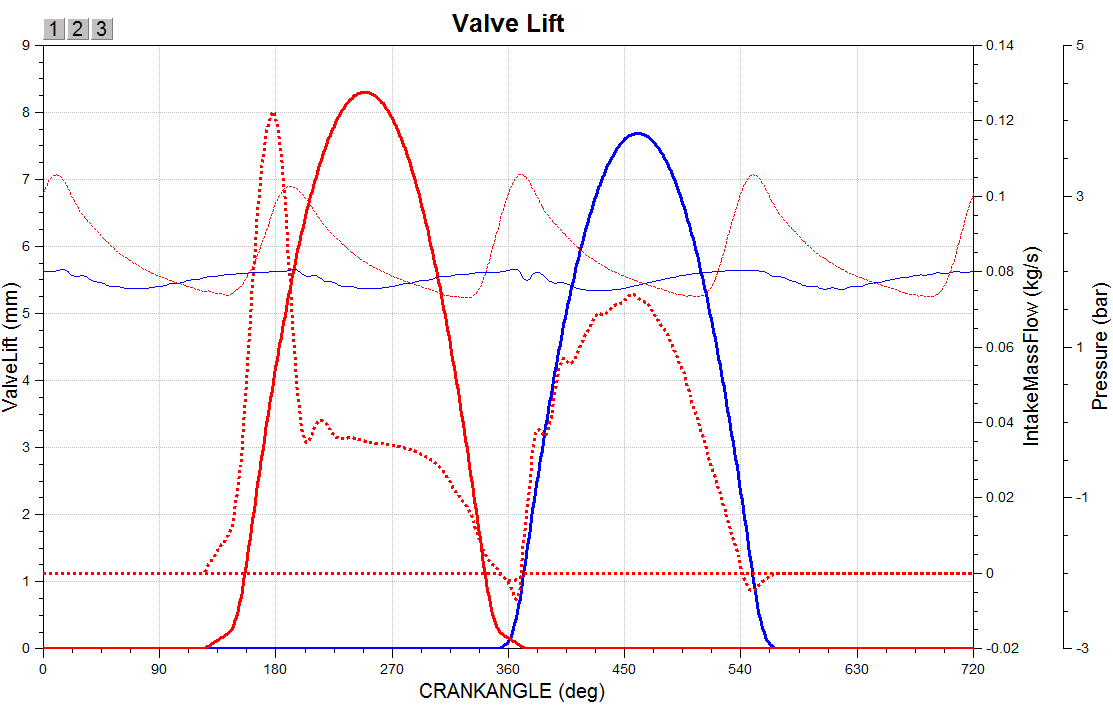
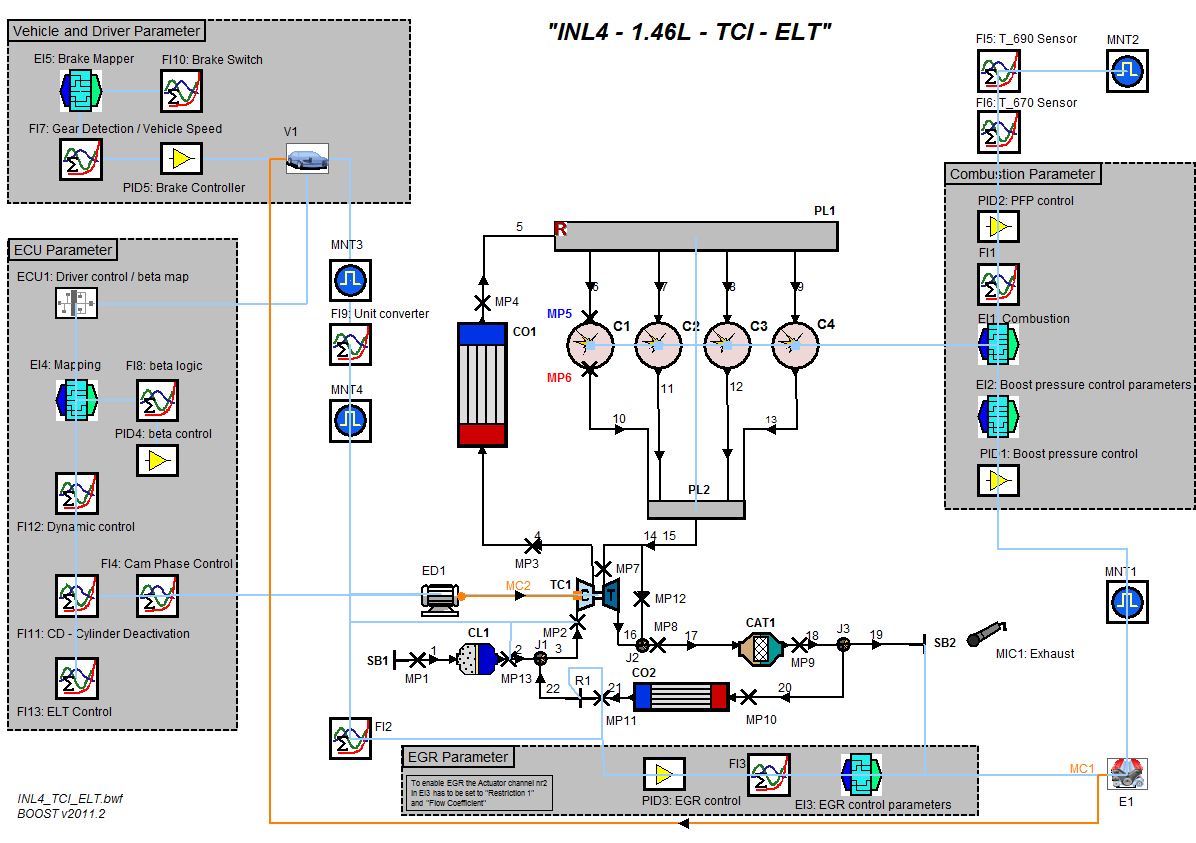
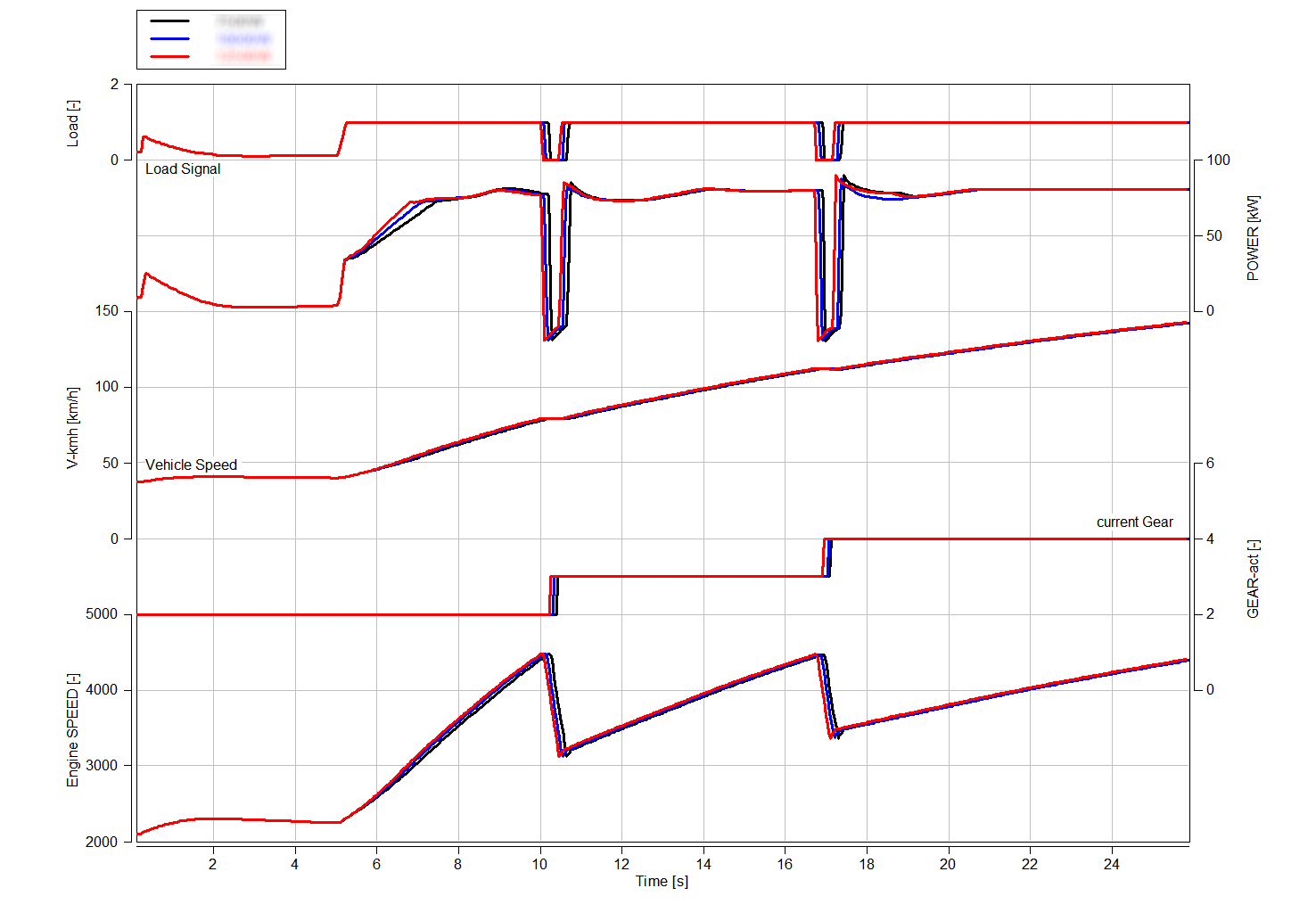
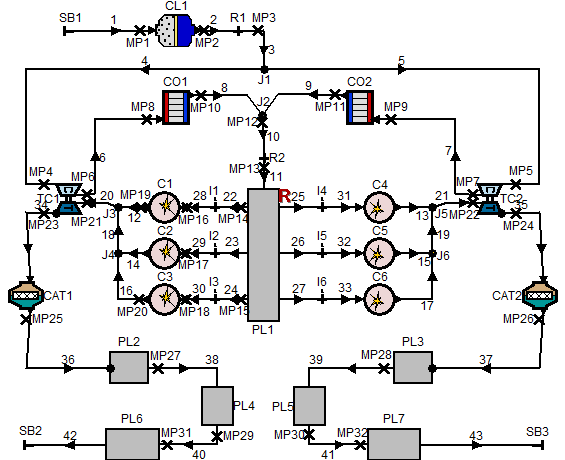
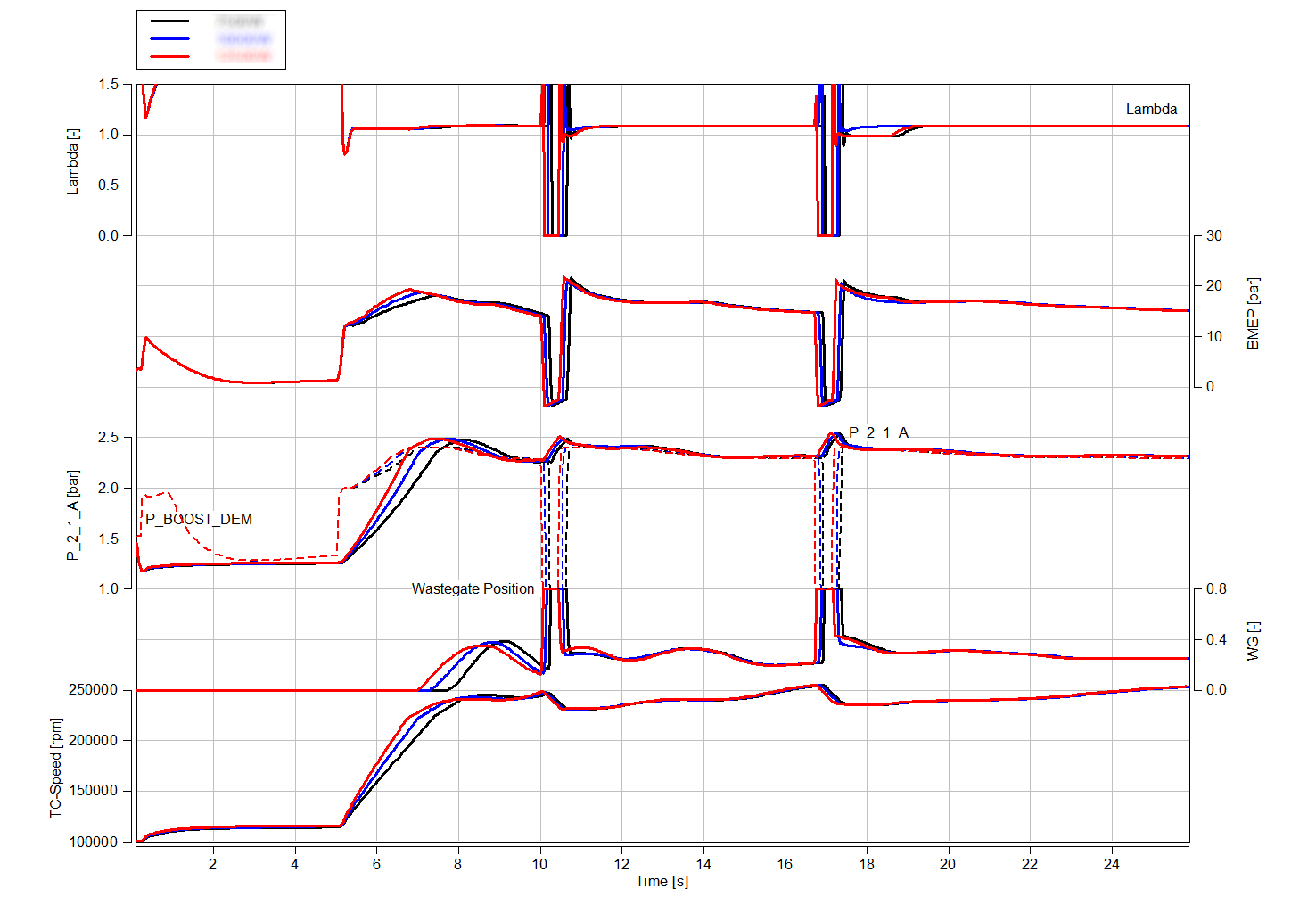
3D-Simulation
The use of 3D-CFD Simulation allows a detailed analyses of complex issues and processes within an engine.
Typical scope of work:
Inlet and outlet port
- Discharge coefficients (µσ, αK)
- Swirl and tumble
Combustion simulation of engines
- BMEP, IMEP, BSFC, etc.
- Ignition delay
- Emissions
- Knocking behaviour, knocking probability
Injection system
- Spray distribution
- Mass flow
- Cavitation